EVA Packaging Lining Guide: Materials, Advantages, Processing & Designs
EVA lining refers to a product placed in an EVA box, which then requires additional box packaging around it, such as a metal tin, white cardboard box, paper box, or aluminum box. Today, let’s discuss the materials, advantages, processing, and designs of EVA packaging lining design.
Introduction to EVA Materials
EVA, made from EVA raw materials, colorants, foaming agents, etc., is formed through high-temperature foaming. There are different types of EVA based on foam characteristics, including environmentally friendly coarse-cell EVA, regular EVA, food-grade odorless environmentally-friendly EVA, fire-resistant EVA, and EVA. By processing EVA sheets, they can be made into EVA inserts, EVA trays, and EVA linings. In terms of hardness, there are regular hardness 38-degree EVA linings, slightly harder 50-degree linings, and even harder 70-degree linings. In terms of performance, there are regular environmentally friendly EVA linings, fire-resistant EVA linings, and EVA linings. EVA linings can be black, white, or colored. They are also referred to as EVA inner boxes or EVA trays.
- Die-cutting:
EVA linings and trays can be formed through die-cutting using either traditional molds or modern computer cutting. Some may require manual assembly after cutting. - Carving:
Using machinery like carving machines for integrated molding.
Characteristics of EVA Packaging Lining
- EVA material is selected based on the total thickness of the product, aiming to keep the material as a single piece rather than multiple layers glued together.
- The internal structure can be programmed to match the shape and size requirements of the product.
- The dimensions are adjustable, with varying depths and hole sizes, such as slot sizes as small as 1.5mm and groove depths as shallow as 0.5mm. The maximum depth can reach around 120mm.
Processing of EVA Packaging Lining
The processing has overcome the traditional practice of repeated stamping and manual layering due to variations in depth. Manual assembly of EVA boxes can result in uneven appearance and distortion of the outer interface, affecting the overall quality when using materials thicker than 20mm. EVA lining processing provides excellent shock absorption, cushioning, seismic resistance, shaping, and moisture resistance. It is widely used in custom packaging boxes for medical instruments, liquor, health products, cosmetics, hardware tools, electronic products, gifts, laboratory instruments, and other products.
Designs of EVA Packaging Lining
- Protection:
Given the various hazards during the transportation of goods, packaging designers need to consider the protective function of the packaging in order to ensure that the products are not affected by external forces. EVA lining, as a common packaging product, is primarily designed with protection in mind. - Convenience:
If packaging materials only prioritize safety without considering convenience, it can lead to significant resource waste. Convenience becomes an important factor when considering the transportation process and user experience. Heavy and unwieldy products increase the cost and burden of shipping. Therefore, convenience is the second important factor when designing EVA packaging lining. - Sales Appeal:
A visually appealing product will capture more attention compared to a dull one. Quality alone does not guarantee sales, as competitors can also offer high-quality products. Investing in the appearance of the product is essential to create a positive first impression. For instance, using plush EVA lining with its soft touch and upscale appearance can enhance the product’s image and provide a better user experience. Many jewelry stores use plush EVA foam lining for this purpose.
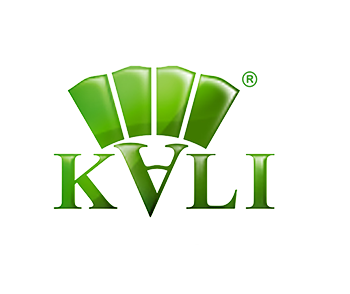
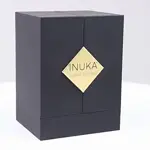
Top 10 Creative Cosmetic Packaging Design Ideas & illustrations 2023 | Luxury-Paper-Box.Com
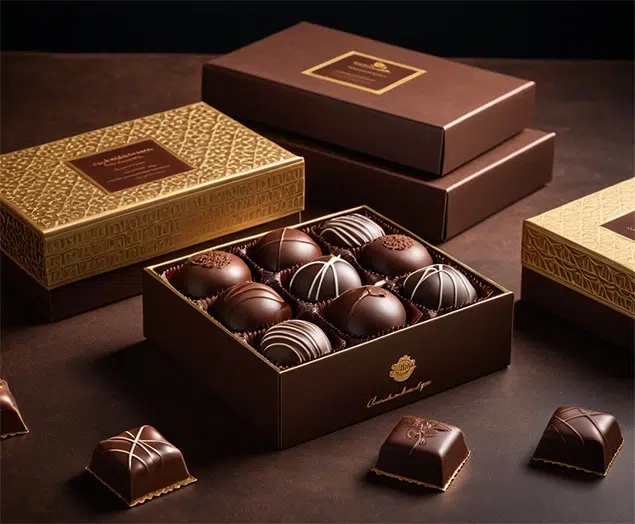
Best Chocolate Packaging Designs of 2025
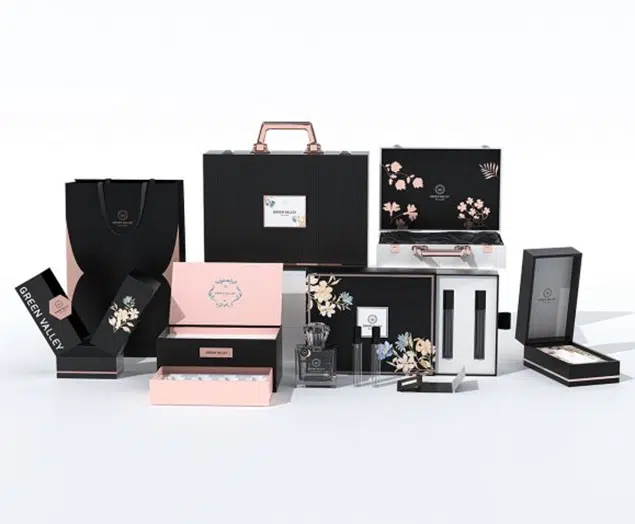
Perfume Packaging Design Trends 2025
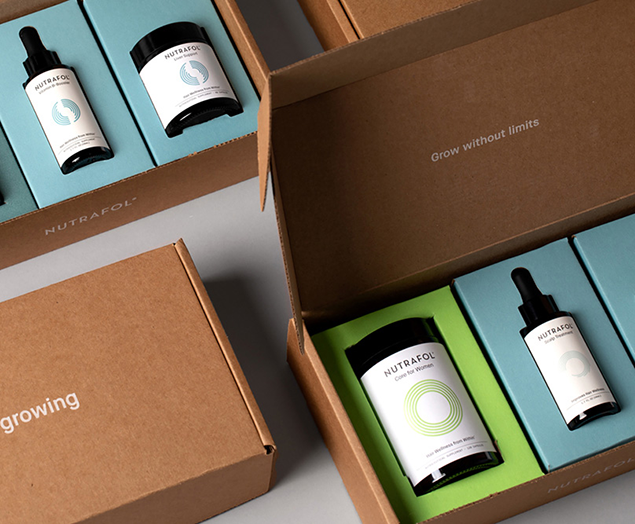
How E-commerce Packaging Wins Hearts (and Wallets)
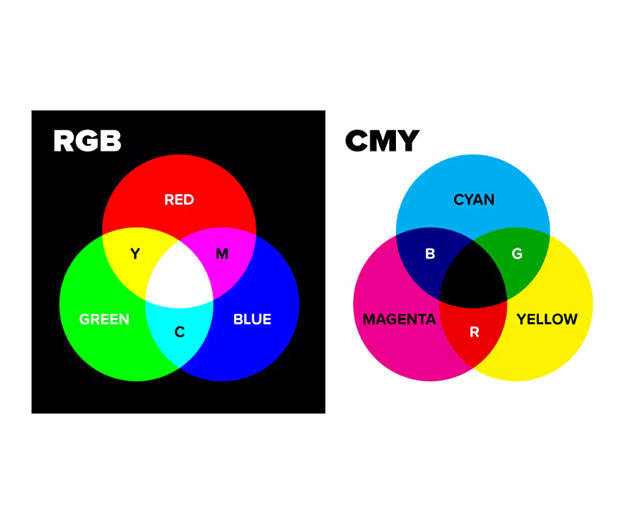