How to Make MDF from Wood Waste in an Environmentally Friendly Way?
Summary
Every year, approximately 30 million tons of wood waste are generated globally, posing a severe environmental threat if not properly handled. However, thanks to advanced recycling technologies, this waste can be converted into versatile MDF (Medium-Density Fiberboard) panels, widely used in construction, furniture manufacturing and packaging industry like laser cut mdf boxes. The process includes wood collection, sorting, shredding, screening, drying, mixing, hot pressing, and surface treatment. Additionally, recycling pallets reduces carbon dioxide emissions and helps conserve forest resources. This cycle not only effectively utilizes resources but also takes responsibility for the future, playing a crucial role in promoting sustainable development.
Global Wood Waste & Recycling Stats
How is MDF recycled by Wood Waste?
Uncovered 30 million tons of wood waste is generated worldwide every year. If it is not recycled effectively, it will ruthlessly accumulate in landfills, which not only causes waste but also causes environmental pollution. However, thanks to advanced recycling technology, we can transform this abandoned wood into MDF boards. This material is widely used in construction and furniture manufacturing. So how do wooden boards transform into new and shiny products? What is the mystery behind this process? What role does the machinery involved play? Let’s find out. The sources of wood waste are very diverse, it can be demolished buildings or even wooden pallets.
You may think that these woods have no value, but the amazing fact is that they are golden materials in the recycling industry. The collected wood will be sent to a special recycling center and enter the sorting stage. Large recycling plants can handle up to 100 tons of wood waste every day, but in fact only about 80% can be effectively recycled.
Sorting and Selecting High-Quality Wood
After careful sorting, only high-quality wood is selected for further processing. This step significantly reduces time and energy consumption in MDF production by ensuring only suitable material enters the system.
Crushing into Sawdust & Metal Separation
The selected wood blocks are crushed into small particles, forming a continuous stream of sawdust. This sawdust is then passed through a magnetic separator, which effectively removes any metal impurities to ensure the resulting material is clean and safe for MDF production.
Refining into Micro Wood Fibers
The sawdust is further ground into fine wood fibers. A screening process ensures that only particles smaller than 0.5 mm are retained. This is crucial for meeting the fiber size requirements of MDF boards.
Washing & Final Purification
All remaining impurities are washed away to ensure the final wood fibers are clean and pure. This step is considered one of the most critical in the entire recycling process, directly affecting the strength and consistency of the final MDF product. A standard plant can process up to 10 tons of wood per day at this stage.
How is MDF recycled by Palette?
Step 1: Robotic Disassembly and Moisture Challenge
Before the wood is chopped, robots efficiently disassemble the pallets, remove nails, and break them down into planks in just a few seconds. However, the wood retains moisture, which can negatively affect MDF production and cause mold if not addressed. Therefore, drying is essential before further processing.
Step 2: Industrial Drying in a Rotating Barrel
A giant dryer, resembling a mobile oven, dries the wood chips. The chips are placed into a large rotating barrel where hot air (150–200°C) is blown in. The rotation ensures uniform drying of each chip. This equipment handles up to 5 tons of sawdust per hour, effectively reducing moisture without burning the wood.
Step 3: Mixing with Branches and Resin Coating
Once dried, branches—important for durability—are added. Urea formaldehyde resin is used due to its strong adhesion, water resistance, and cost-effectiveness. With advanced mixers, stump wood and branches are thoroughly combined within minutes, ensuring each fiber is evenly coated. This stage is key to the MDF board’s strength.
Step 4: Hot Pressing into MDF Boards
The resin-coated wood fibers are then hot-pressed into boards. Under a temperature of up to 200°C and pressure of 30 MPa, the fibers bond tightly in just 5 to 7 minutes. The final MDF boards are formed with a thickness ranging from 6 to 25 mm depending on production needs, completing the transformation from waste wood to a durable material.
What’s the Daily Production of MDF Boards?
A large wood recycling plant can produce up to 100,000 MDF boards per month. After they have been subjected to high pressure treatment and cooled, they need further surface treatment. At this point, the boards are cut into standard sizes and sanded to make the surface smoother. Industrial tools cut them into regular sizes, usually 1.2 meters by 2.4 meters, for the application of MDF or plywood. Modern cutting machinery can process multiple boards at the same time, ensuring that each size is consistent, thereby improving production efficiency. After cutting, the boards are then polished by a sander, which moves at high speed to remove the rough parts of the surface and leave a smooth surface. This process is an important part of ensuring the quality of the board.
How to Optimize MDF Production Efficiency?
If you have ever experienced sanding wood by hand, you will understand that this task is tedious. However, these industrial sanding machines can complete the work of hundreds of craftsmen in just a few minutes. Although the journey of the MDF board is coming to an end, there is still one last step, surface treatment. By coating the MDF board with a layer of melamine or thin wood veneer, a beautiful and protective surface is added. This not only improves the appearance, but also prevents environmental damage to the board, such as scratches or moisture. After surface treatment, the service life of the board can be extended by 30%, while adding visual appeal to the product. Large factories are able to process thousands of board surfaces with high precision every day.
Why is MDF good for the environment?
Compared with production, new wood boards are an important part of combating climate change and protecting forest ecosystems. Every piece of wood, no matter how small, can contribute to a sustainable future as long as we know how to use it. Recycling is not only about reusing materials, but also a symbol of innovation, creativity and responsibility for the future. We recycle not only wood, but also give the next generation hope for a cleaner and greener future.
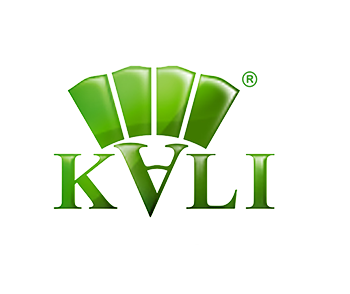
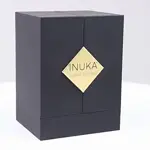
Top 10 Creative Cosmetic Packaging Design Ideas & illustrations 2023 | Luxury-Paper-Box.Com
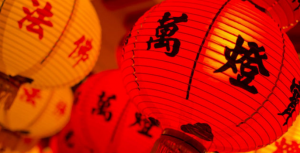
10 Customs Of The Spring Festival (Lunar New Year) You Need To Know
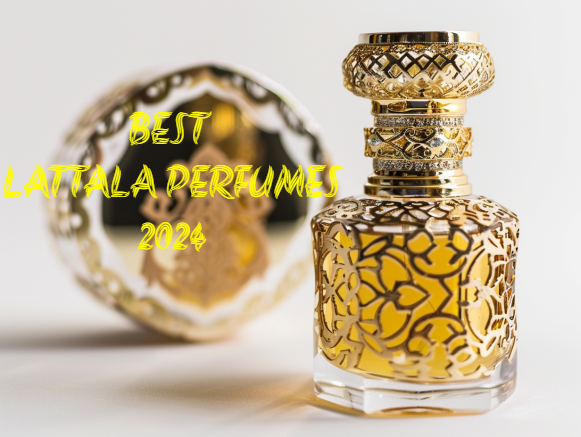
Top 10 Best Lattafa Perfumes for Women & Men in 2024
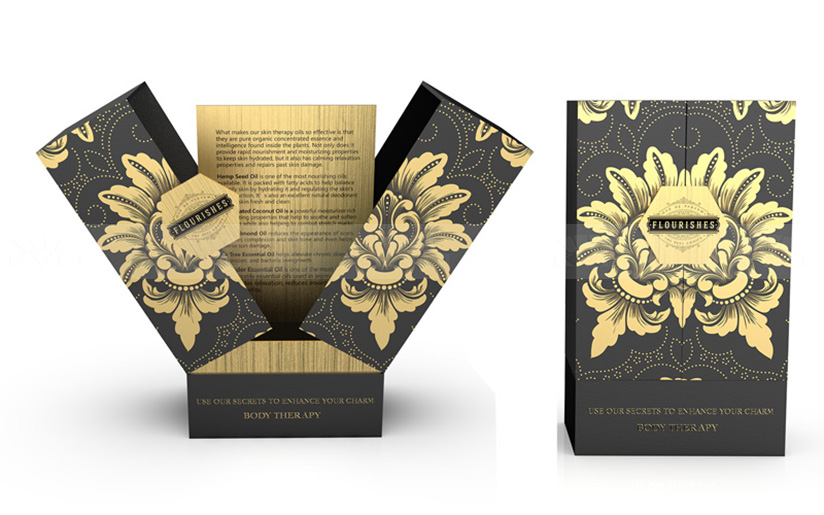
Top 10 Best Packaging Design Software 2023 (Free & Paid)
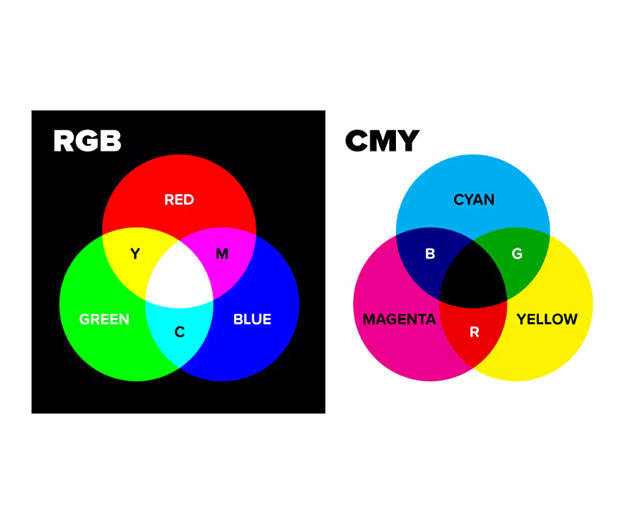