Wrapping Machine Guide (Box): Types, Functions, Maintenance & How to Choose
The role of packaging box machinery becomes a critical element. From weighing and filling to sealing and labeling, packaging machinery plays a pivotal role in enhancing production efficiency and ensuring the quality of goods. In this box wrapping machine guide, we delve into its types, functions, maintenance & tips to pick.
Wrapping Machine Guide (Box): Types, Functions, Maintenance & How to Choose
Packaging wrapping machinery refers to machinery that can complete all or part of the product and commodity packaging process, mainly completing processes such as weighing, filling, wrapping, sealing, as well as related pre – and post processes such as cleaning, stacking, and dismantling; In addition, measurement or stamping on packaging can also be completed. Using mechanical equipment to package products can improve production efficiency, reduce labor, directly improve the economic benefits of enterprise production, meet the needs of mass production and manufacturing, and meet the standards of environmental cleanliness. In the continuous and large-scale industrial production process, packaging is the last step. Packaging can play a role in protecting, beautifying, promoting, and selling products, improving the competitiveness of goods, achieving packaging automation can effectively improve production capacity, ensure product quality, and help reduce production costs. Packaging automation is the use of automation devices to control and manage the packaging process, making it automated according to predetermined procedures.
Packaging Wrapping Machine Type
The commonly used classification method is based on the packaging process, which can be divided into important packaging machines and auxiliary packaging machines. The packaging machine that implements packaging processes such as wrapping, filling, and filling is called a critical packaging machine, or a packaging host; The packaging machine that realizes washing, drying, inspection, stamping, measuring, conveying, and stacking is called an auxiliary packaging machine.
Wrapping and packaging machine
Wrapping packaging machines are used to package block shaped products. According to the different packaging processes, they can be divided into twisted packaging machines, end folding packaging machines, pillow packaging machines, envelope packaging machines, stretch packaging machines, etc.
Filling and packaging machine
Filling and packaging machines are used to package solid items in powder and granular form. Filling packaging machines include two types: crisp filling packaging machines and bag making filling packaging machines. Simply filling packaging machine is used to fill pre formed plastic or paper bags, or simply fill other containers. The bag making and filling packaging machine is a packaging machine that requires both the molding of the container and the filling of the product into the container.
Filling and packaging machine
Filling and packaging machines are used to package fluid and semi fluid items. According to the process of filling products, they can be divided into atmospheric pressure filling machines, vacuum filling machines, pressurized filling machines, etc. Filling and packaging machines, along with sealing machines, labeling machines, etc., continue to become a mechanized filling water line.
Sealing machine
The sealing machine is suitable for sealing various packaging containers. According to the different sealing processes, it can be divided into glass jar capping machines (such as capping and rotary capping), bag mouth sewing machines, box sealing machines, various sealing machines for plastic bags and paper bags.
Labeling machine
Labeling machine is a machine used to stick label paper or labels onto packaging.
Tie down the machine
There are various types of tying machines, including belt tying machines, wire or rope tying machines, etc.
Mature packaging machine
Mature packaging machines are divided into blister packaging machines and close fitting packaging machines according to the difference in processing technology.
Vacuum packaging machine
Vacuum packaging machines can be divided into two types: vacuum packaging machines and inflatable packaging machines, based on whether they can charge inert gas after vacuuming.
Compression packaging machine
In addition to small compression packaging machines that can be used for single or multiple product sales packaging, there are also large compression packaging machines that can be used for transportation packaging including pallets.
Other packaging machines
In addition to the above types of packaging machines, there are also bottle washing and drying machines, packaging material and specification inspection machines, stamping machines, measuring machines, etc. These single machines are combined with other packaging machines to form a packaging unit.
Commonly seen packaging machines:
Bag making, filling, sealing and packaging machine
The key processes of bag making, filling, sealing, and cutting packaging machines include bag forming, filling, sealing, and cutting. The accepted packaging materials should be film products, such as plastic film, paper, lead foil, and composite film.
Hot forming packaging machine
Thermoforming packaging machines can be divided into blister packaging machines and close fitting packaging machines based on the differences in packaging container forming processes. Bubble wrap packaging is currently a widely used type of packaging. It is a packaging method that seals the product between the preformed blister and the bottom plate. Body to body packaging and bubble wrap packaging are similar, with the difference being that the products in body to body packaging are used as forming molds, while bubble wrap packaging is formed using specialized molds. Close fitting packaging can fix the product in place, ensuring that the product quality is not damaged due to collision during circulation.
A compression packaging machine is a packaging machine that uses hot compressed film that is oriented through stretching to package items (or inner packaging), and then heats the film appropriately to compress the film and tightly wrap the items (or inner packaging). The compressed film is tensioned by the high and low rollers, and the product is pushed towards the film by machine components. After the film wraps the product, the three sides of the film are sealed by the sealing component, and then transported by a conveyor belt through a heating device, Prohibited from wrapping products, cooled to form compressed packaging
How to Choose the Type of Packaging Machine
1. Technical parameters: Firstly, we need to pay attention to the technical parameters of the vertical packaging machine, such as packaging speed, packaging accuracy, packaging range, etc. These parameters are directly related to the performance and efficiency of the packaging machine. Generally speaking, the higher the technical parameters, the better the performance of the packaging machine.
2. Machine material: The material of the vertical packaging machine directly affects its durability and stability. High quality packaging machines are usually made of stainless steel or other wear-resistant and corrosion-resistant materials, which can ensure good performance during long-term use.
3. Control system: A good vertical packaging machine should be equipped with advanced control systems, such as PLC control systems. This system can achieve automated operations, improve packaging efficiency, and also facilitate operator debugging and maintenance.
4. After sales service: When choosing a vertical packaging machine, we also need to consider the manufacturer’s after-sales service. The service life of a machine is usually 5-10 years, and good after-sales service can solve problems in a timely manner to avoid affecting production.
5. User reviews: Finally, we can understand the actual performance of vertical packaging machines by reviewing user reviews. User feedback is often more authentic and reliable, allowing for an understanding of the advantages and disadvantages of the machine.
How to Use a Packaging Wrapping Machine?
1. Place packaging machine materials
Firstly, we need to prepare the materials for the packaging machine, such as your product, your packaging container, and product materials, and place them in the corresponding positions for the normal use of the packaging machine. It should be noted that before using the packaging machine, it is necessary to ensure its cleanliness and hygiene, especially for packaging machines with filling technology, which can easily accumulate dirt and cause secondary pollution of the product. In addition, the packaging container should be suitable for the specifications and dimensions of the packaging machine.
2. Turn on the power switch of the packaging machine
After we have prepared the materials and containers used in the packaging machine, we will turn on the power switch and the packaging machine will officially start It should be noted that before turning on the power switch of the packaging machine, the power line needs to be checked. If there is any exposed area on the power line, it is necessary to replace it in a timely manner, otherwise there is a risk of electric leakage, and it is also very easy to damage the packaging machine equipment.
3. Packaging machine parameter settings
After the power supply of the packaging machine is turned on, the touch screen of the packaging machine will also start. We need to click to enter the parameter settings of the packaging machine, and set parameters such as temperature, sealing time, sealing speed, filling capacity value according to the packaging machine manual to ensure the normal use of the packaging machine. It should be noted that the parameters of the packaging machine must be set according to the instructions of the packaging machine. For example, the sealing temperature of the packaging machine is 200 degrees. If the set temperature is below or above 200 degrees, there may be bubbles in the sealing or the sealing film may not be correct.
4. Starting the packaging machine
After everything is ready, the packaging machine can be officially started. Simply press “Start” on the main menu, and the packaging machine can operate normally! During the startup process of the packaging machine, we should always observe the temperature of the machine. If the temperature is too high, we should stop the operation and wait for the packaging machine to cool down for half an hour before proceeding with the operation to avoid equipment failure caused by excessive temperature. In addition, if there is any abnormal noise during the operation of the packaging machine, it should be immediately shut down and restarted after inspection and maintenance.
How to Maintain the Packaging Wrapping Machine?
The key points of maintenance and upkeep for packaging machinery include cleaning, tightening, adjustment, lubrication, and corrosion prevention. In the normal production process, each machine maintenance personnel should strictly follow the maintenance manual and procedures of the machine packaging equipment, strictly carry out various maintenance work within the prescribed cycle, reduce the wear rate of parts, eliminate hidden dangers of faults, and extend the service life of the machine.
Maintenance is divided into routine maintenance and regular maintenance (divided into first level maintenance, second level maintenance, and third level maintenance)
Special maintenance (divided into seasonal maintenance and out of service maintenance) focuses on cleaning, lubrication, inspection, and tightening. Routine maintenance should be carried out as required during and after machine operation. The first level maintenance work is carried out on the basis of routine maintenance, with a focus on lubrication, tightening, and inspecting all relevant parts and their cleaning work. The second level maintenance work focuses on inspection and adjustment. Specifically, check the engine, clutch, transmission, transmission components, steering, and braking components. The focus of Level 3 maintenance is to detect, adjust, eliminate potential faults, and balance the wear and tear of each component. Diagnostic testing and status checks should be conducted on parts that affect the performance of the equipment and those with signs of failure, in order to complete necessary replacement, adjustment, and troubleshooting work.
Seasonal maintenance refers to the inspection and repair of components such as the fuel lubrication system, hydraulic system, cooling system, and starting system of packaging equipment before the start of summer and winter each year.
Stopping maintenance refers to cleaning, cosmetic surgery, matching, and anti-corrosion measures taken when packaging equipment needs to be stopped for a period of time due to seasonal factors (such as winter vacation).
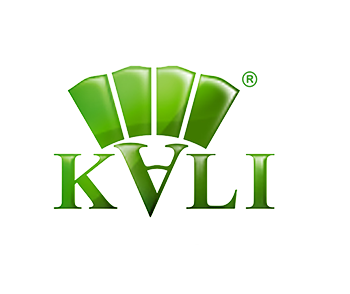
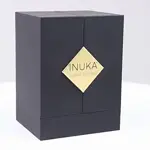
Top 10 Creative Cosmetic Packaging Design Ideas & illustrations 2023 | Luxury-Paper-Box.Com
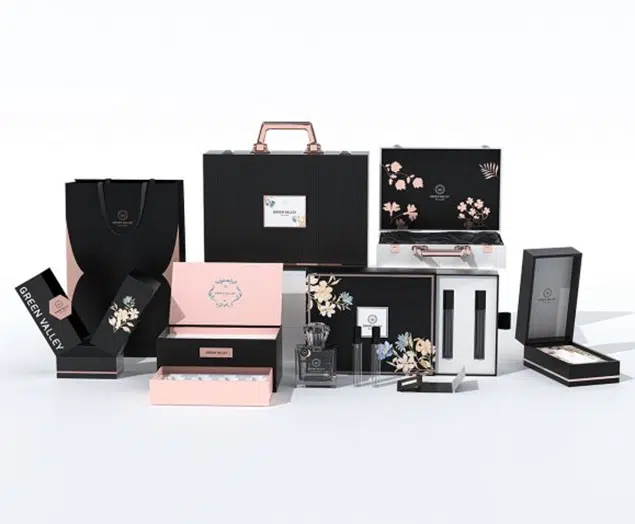
Perfume Packaging Design Trends 2025
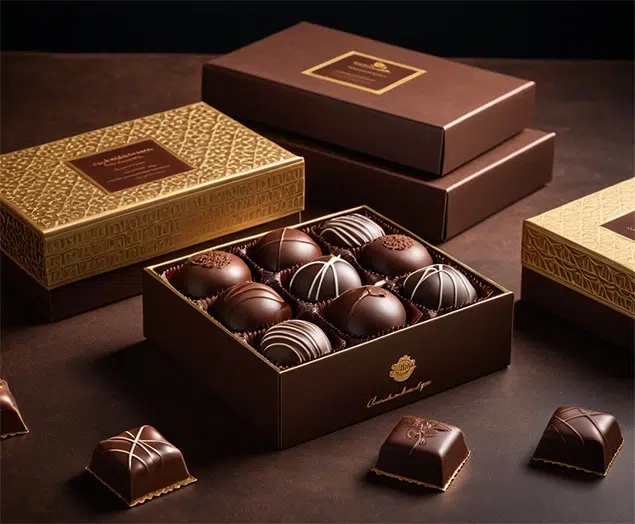
Best Chocolate Packaging Designs of 2025
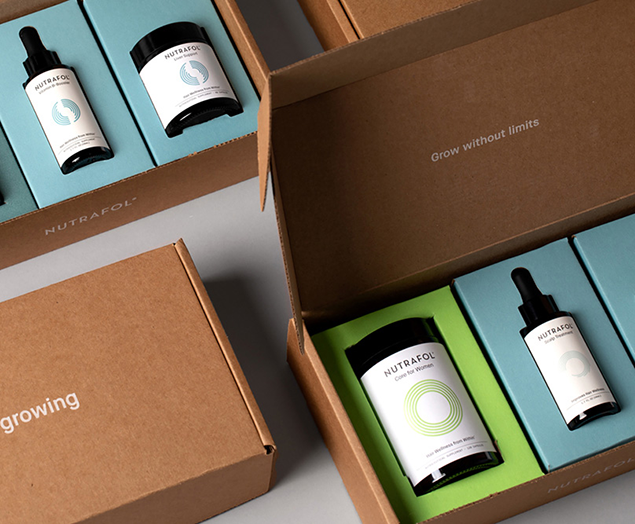
How E-commerce Packaging Wins Hearts (and Wallets)
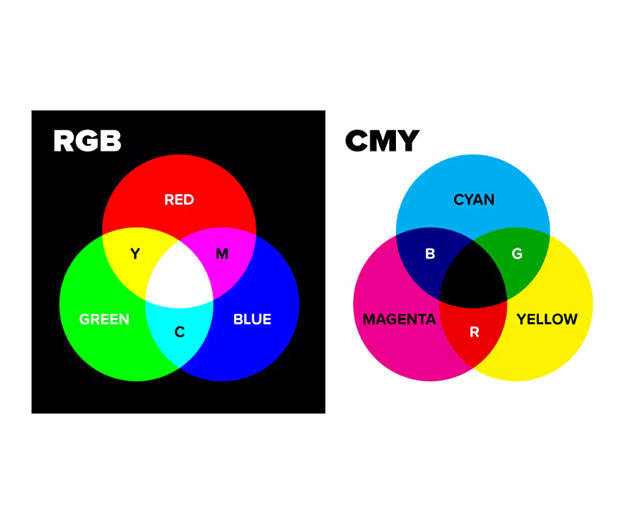