8 Best Packaging Printing Tips – How To Make Perfect Box Printings
This type of printing uses a variety of packing materials as the medium. Patterns, phrases, and other visual elements are used to enhance the product’s visual appeal and convey information, and improve sales. Including the printing of packing cartons, bottles, cans, and other packaging materials. Packaging printing is an essential aspect of packaging engineering and is widely used in the printing and packaging industries. In this guide, we are going to show the best tips and tricks to create perfect packaging printings.
8 Packaging Printing Tips You Should Be Aware Of
1.Pay attention to the observation examples.
Packaging and printing quality control sampling. Shortly after the announcement of packaging and printing, the ink and water supply flow indicated at the commencement of printing will be revised. Performing regular sampling inspections and readjustments is critical. Samples should be inspected at a rate of 500-1000 per print if the printing rate stays constant and the ink and water supply flows are consistent. Printed goods plant in Nanjing
Clip the cautionary message in. Long and thin warning strips should be clamped in the regions where common defects occur during the announcement packing and printing as a mark to simplify examination in the succeeding process flow.
2. Keep an eye on the inflow of water to see whether it changes.
In the early stages of packing and printing, pay attention to the change in water intake. During the trial printing and after the package and printing are announced, the water filling flow will change. The water supply flow of the printing plate should be monitored while you look at the samples to see whether there are any overlaps or water carriers.
Keep an eye out for any water changes during the packing and printing process. Keep a tight eye on the equipment’s main body and the natural ventilation in the manufacturing workplace for water ingress to see if they do any damage. Control the temperature of the wetting liquid and the cooling equipment in the wetting system software while using the ethanol dampening plate. The printing plate will get unclean if there is not enough water flowing into it, and if there is too much water, printing ink emulsion will form, resulting in a slew of issues. Some examples include faint print, retractable print paper, and a delay in the drying time of printing ink.
3. Pay close attention to the ink replacement cycle.
The printing ink in the ink bucket line is important. A natural extrusion occurs when the weight of the printing ink in the ink bucket line passes through the space between the roller and scraper. Because of this, the amount of printing ink in the ink bucket line will have an instantaneous effect on the production of printing ink. Consequently. Maintaining a sufficient supply of printing ink is essential, so keep an eye out for it. Ink printing also has the advantage of being compressible. The fluidity will gradually decrease if it is left in the ink bucket line for an extended period of time. As a result, it is sometimes essential to utilize an ink knife or a printing ink mixing equipment in the ink bucket line to mix the ink.
Printing ink should not dry on equipment. The printing ink on the ink roller and the printing ink surface in the ink bucket line will be dry if the machine is shut off for an extended period of time, such as when eating or sleeping. To avoid dryness, it can be sprinkled on the area.
Keep an eye out for the symmetry of the ink that is used in printing. The water flow, temperature, and speed of the printing equipment all have an effect on the density of printed materials. The standard samples should be compared often to this one. Avoid using ink that has luminous spots on it.
The wetting solution’s pH should be kept constant. Changing the pH value of the wetting solution after the printing ink has been neutralized is quite straightforward. As a result, it is important to keep an eye on the pH value to prevent the printing plate from becoming unclean.
4. Pay attention to the dirt on the back of your hands.
Reverse-side dirt accumulates owing to printing ink adhering to previously printed reverse-side ink due to long drying time of ink, thick graphic ink layer, and high smoothness of paper during printing.
5. Keep an eye out for shadows that overlap.
Superimposed images are caused by printing plates shifting the images they produce, causing two-way and triple image shadows to appear in the printouts. Ink, paper, teeth, barrels, screen printing ink, printing speeds, and ink viscosity are just a few of the more complicated aspects that can cause printing to overlap. To find out what’s causing the problem and fix it, use one of the options listed below.
First, open and print a second time to make sure that the print quality is accurate, as well as to test the paper pulling force and adjust the paper feeding mechanism, paper pressing wheel, and pressing components.
To determine if the silk screen printing ink has sufficient holding power, perform step 2. Using the new ink for silkscreen printing is a breeze. Avoid overtightening by following the step-by-step tightening procedure.
Verify the operating pressure of barrel lining and printing on packaging boxes.
Inquire whether the printing paper is appropriate. In particular, printing paper with wavy lines at its mouth is prone to overlap pictures, which necessitates thorough scrutiny of the finished product.
Reduce printing ink viscosity. Because of the ink’s high viscosity, it’s difficult to separate the printing paper from the screen printing ink, causing the trailing tip to become unstable and cause overlapping. Printing ink’s viscosity can be somewhat reduced by using this additive.
The gripper may be adjusted. The major cause of the overlap is a lack of teeth correction and care. For this reason, it is critical that dental work such as adjusting, cleaning, and inspecting be done on schedule.
6. Printing quality should be checked at this point, as well.
Run another 20 to 30 pieces of printed material through the machine, twist the paper a little after running, and check the front and side gauges to make sure they are properly positioned (able to carry out two printing inspections).
7. Pay close attention to the total quantity of copies.
Prior to completing the package printing process, it will be checked to see if the printing number matches that of the packaging itself. The production and manufacturing management will be informed if there is a shortfall in the supply and the supplement will be given as soon as possible.
8. Don’t forget about other projects.
The process of adding ink and wetting liquid to the container.
Work on two projects. Because printing plates and screen printing ink collect dirt, such as leather residue, paper powder, and paper wool, and reflect it onto the printing paper, it is necessary to clean printing plates and screen printing ink. In most cases, the equipment must be shut down before the dirt removal may begin. Unless special equipment is available to clean the machine while it is in use. During the course of surgery, it is absolutely banned to remove dirt.
Dispose of used screen printing ink and eraser. The machine should be stopped if printing ink, paper powder, or powder spray powder is deposited on the silk screen printing ink, putting the printing ink migration at risk. Dispensing and editing will also be secure.
Pay attention to printing equipment malfunctions. Keep an eye out for any abnormalities in the printing equipment’s functioning and pay attention to any noises or vibrations that may be coming from the machine.
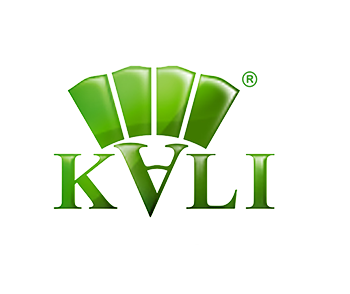
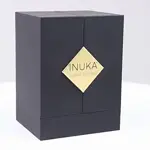
Top 10 Creative Cosmetic Packaging Design Ideas & illustrations 2023 | Luxury-Paper-Box.Com
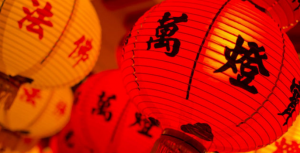
10 Customs Of The Spring Festival (Lunar New Year) You Need To Know
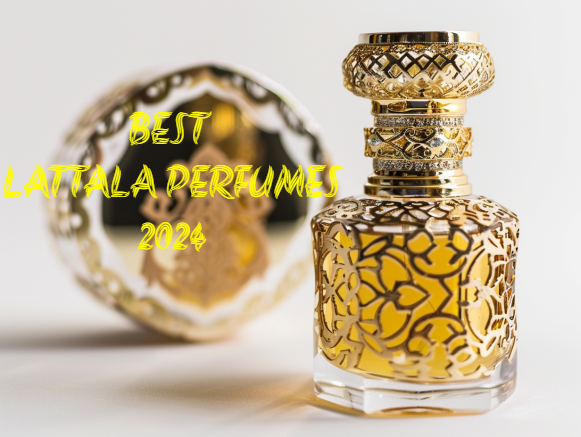
Top 10 Best Lattafa Perfumes for Women & Men in 2024
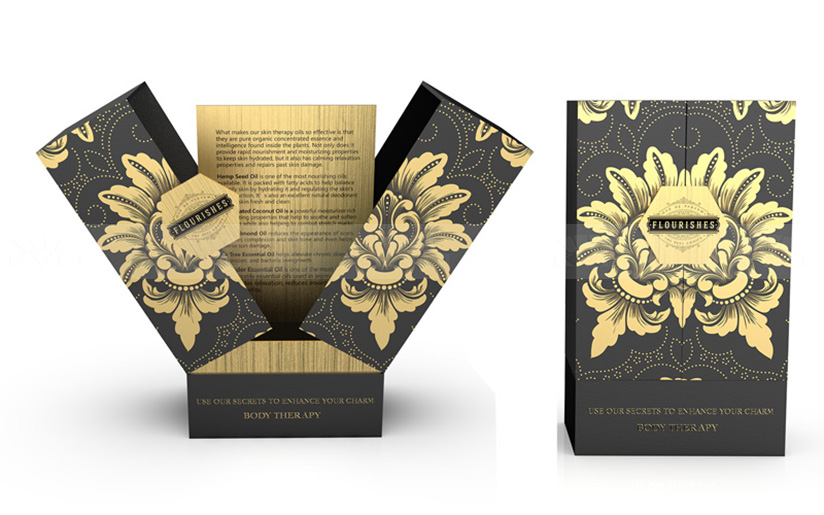